Root Cause Analysis (RCA)
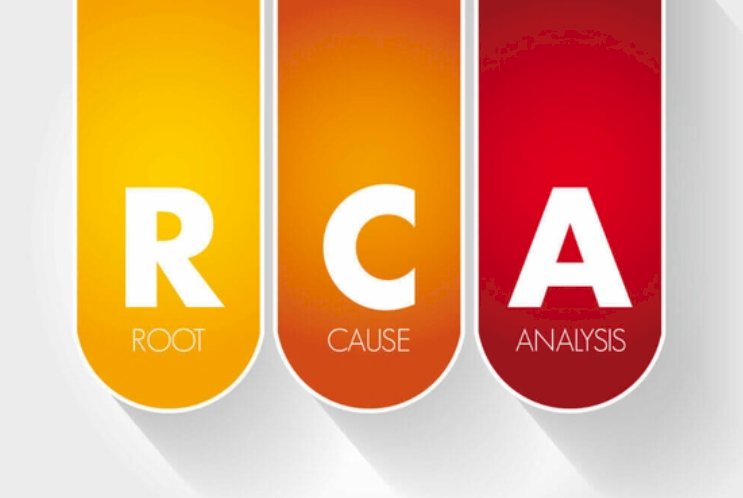
Root cause analysis (RCA) is a problem-solving approach that identifies the fundamental reason behind any problem or situation. It helps to arrive at an optimum solution by bridging the cause-and-effect relationship for an event.
How does Root Cause Analysis Work?
Root Cause Analysis refers to finding the crux of a problem. It is used as an umbrella term to refer to various tools and techniques applied to solve the problem. This approach is applied across different industries, from healthcare and software to environment and manufacturing.
It is one of the popular methods among scientists and engineers to resolve various technical issues. At the same time, IT professionals commonly apply it to narrow down the source of a bug while coding.
In business, it is one of the most critical aspects of quality control in any organization. It helps identify the core problems in the products, processes, systems, and financial performances. Recognizing the exact cause assists in designing measures to eliminate the loopholes at the right time. Note that there are three possible causes behind any issue: physical, organizational, and human.
One of the extensively used root cause analysis tools is the 5 Whys. Here, the analyst or the team leader raises the question “Why the situation occurred?” And then, in the course of deeper investigation, a sequence of Whys is put forward for the team to find the answers. This continues until the base cause or primary reason is discovered.
Note that there is no limit to asking the Whys in this method. It can even go beyond five questions, depending on the case. Let us understand this concept through an example.
The finance manager of ABC Ltd. found that the cost of manufacturing the products rose by almost 15% in a given year. Therefore, he decided to adopt the RCA method to find the loopholes and reasons behind the high cost. The finance manager raised the following questions under the 5 Whys technique:
- Why did the cost of production upsurge by 15%?
- Why did the raw material become expensive?
- Why didn’t we switch to other suppliers?
While discussing the answers to the above questions, he found that the production cost soared due to the increase in raw material price. In turn, the raw material became expensive because of its shortage and high prices of fuel.
Also, the company didn’t switch to the alternative suppliers due to the benefit of the extended credit period offered by the old suppliers. However, in the long run, the company has the potential to find new suppliers who allow similar privileges.
As evident from the example, the Root Cause Analysis involves identifying a problem and performing a detailed diagnosis. Here, the emphasis is on diagnosis as it helps pinpoint the exact reason for the issue and discover and implement its solution.
Steps of Root Cause Analysis
Below mentioned are some of the steps to be followed in preparing an RCA Analysis Report:
- Identifying and describing the problem: RCA begins with finding the Key Problem Area (KPA) and preparing a detailed description of the problem statements and the events.
- Stating the chronology: Next is arranging the sequence of the events in the order of their occurrence.
- Collecting information: This step is crucial for investigating the problem area. It involves gathering quantitative and qualitative data on pre-event conditions and post-event situations.
- Ascertaining and differentiating casual factors: The analyst then figures out all the possible causal factors responsible for the problem or event’s occurrence. Even the past RCAs can provide essential input at this stage.
- Casual graphing: After listing the identified reasons, these are charted in a graphical format. This helps to visualize the comprehensive information, eliminate possible causes, and conclude the issue’s root cause.
- Determining and implementing the corrective action: Finally, when we are aware of the principal cause, the analyst can chalk out and impose the best possible measures to fix the problem.
Root Cause Analysis Tools
Below mentioned are some of the tools used:
- Pareto Chart – Pareto analysis contends that 20% of factors contribute to 80% of the problems. The Pareto chart is created using the frequency and the causes of the problems. It is a bar chart with a line graph. The bar represents the frequency of the issues that occur, while the graph represents the cumulative percentage of the same.
- 5 Why’s – It refers to asking questions concerning the problem till the key reason for it is unearthed. It starts with the primary query that “Why the problem took place?” Then, it is followed by multiple questions until the reason behind the event is detected.
- Fishbone Diagram – The Ishikawa fishbone diagram figures out the subsequent sub-causes of the original problem, along with the primary source of it. Thus, it helps identify and group possible causes of an issue by relating the cause with its effect.
- Scatter Plot Diagram – Scatter plot diagram is a tool that graphically and systematically presents the numerical data to establish a correlation between two variables for predicting results.
- Flowchart – It is again a form of visual tool that helps an analyst represent and study the different steps involved in a business process. This helps in locating the problem area and its source.
- Fault Tree Analysis – Under this analysis technique, the problem or event is stated on the top-most place of a flowchart. It then sub-divides into multiple minor issues, leading to further classification and finally reaching the base problem.
- Failure Mode and Effective Analysis (FMEA) – It is a method applied to decode the reasons for the possible failure of a particular product or process. Besides, it also ascertains the multi-dimensional impact of such an unsuccessful event.